Milk Tanks and Radar Level Sensor
In dairy industries, it is extremely important in milk storage and transportation processes. The milk storage tanks not only require suitable temperature and pressure, but also accurate level monitoring to ensure high efficiency and safety in production process. The traditional level measurement method (like floats, pressure sensor) often affected by environment factors. It is hard to achieve high precision and highly reliable measurement. Therefore, the use of radar level sensors has become the preferred solution for the modern dairy industry.
Customer Concerns
1.Accuracy: The milk physical properties (eg foam, viscosity changes) may result in inaccurate measurements.
2.High hygiene requirements: The dairy industry has extremely high hygiene standards, and traditional liquid level gauges may be difficult to clean, increasing the risk of contamination.
3.Difficult to maintain: The storage tanks is often located on inaccessible location, making maintenance and debugging of traditional level gauges difficult.
4.Environmental adaptability: The storage tanks may locate outdoor. The device is required good level of protection against harsh weather.
Product Recommendation
To solve the above problems, we recommend customers to adopt radar level sensor with Bluetooth debugging function, it has built-in Bluetooth module, which supports wireless connection and debugging, making it easy to install and maintain on site. The protection grade reaches to IP68, so it is suitable for harsh environment. The radar level sensor measure liquid level by emitting microwave signals and receiving reflected signals. They are not affected by medium characteristics (such as density, viscosity), and non-contact measurement avoids the risk of contamination. The radar level sensors measure liquid level by emitting microwave signals and receiving reflected signals. They are not affected by medium characteristics (such as density, viscosity), and non-contact measurement avoids the risk of contamination.
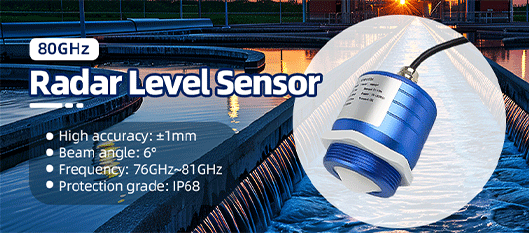
Customer Application Solution
Customer Background
A customer in an Australian dairy farm, which has 5000 cows, the average daily milk production is about 80 tons. Milk needs to be temporarily stored in stainless steel storage tanks (capacity 50m³) before being transported to the dairy processing plant. And because of the remote location, the equipment needs to be able to withstand harsh environments (high temperature, rain, dust).
Customer Pain Points
1.Large measurement error: the traditional float level gauges cause data fluctuation because of milk foam and consistency changes.
2.High maintenance costs: The storage tank is located outdoors. Frequent maintenance requires shutdown operations, which affects production efficiency.
3.Hygiene risks: Contact sensors are prone to residual milk stains, are difficult to clean, and pose potential contamination risks.
4.Inconvenient debugging: The height of the storage tank is 6 meters, and manual climbing for debugging is time-consuming and poses safety risks.
Solution Introduction
Adopts GLT744 80GHz high frequency radar level sensor, supports Bluetooth debugging function, the protection grade is IP68.
Installation location: At the top center of the tank, points vertically to the liquid surface and avoids the top of the agitator (to reduce eddy current interference).
Signal processing: The built-in algorithm filters out the liquid level fluctuation interference caused by the stirring blades.
Communication link: The liquid level data is transmitted to the farm central control system through the 4G module and backed up to the cloud simultaneously.
Core advantages:
Non-contact measurement: Avoids contacting with milk, and risk of contamination.
Anti-interference:High-frequency microwave penetrates the foam and accurately measures the actual liquid level.
Bluetooth wireless debugging: Remotely configure parameters through the mobile APP, no need to climb the tank.
Program effect
This solution uses non-contact high-frequency radar + Bluetooth wireless technology to overcome the accuracy, hygiene and maintenance problems of liquid level measurement in the dairy industry. It is suitable for tank monitoring scenarios of media with high hygiene requirements such as milk and cream. In the future, it can be expanded to integrated monitoring of multiple parameters such as temperature and density to promote the intelligent upgrading of the dairy industry.