Industrial Background
Natural gas pipeline pressure monitoring is the core link in ensuring the safety of energy transportation.
As the global energy structure shifts towards cleaner, natural gas consumption continues to grow, and the long-distance, high-pressure gas pipeline network is expanding rapidly. In terms of industry characteristics, abnormal pipeline pressure may cause major accidents such as leakage and explosion. For example, in 2023, a methane leak caused by uncontrolled pressure in a pipeline in North America caused serious ecological impact. In the future, with the development of intelligence, pressure monitoring technology will continue to evolve towards multi-media compatibility, digital twins, etc.
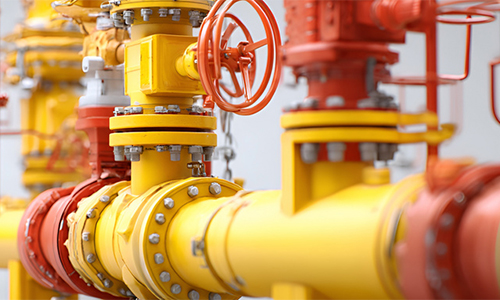
Pain points
Insufficient environmental adaptability: The temperature difference along the pipeline is large, and traditional sensors are easily affected by temperature drift, resulting in data distortion.
High safety risk: Natural gas is flammable and explosive, sensors must comply with explosion-proof certification, and ordinary equipment has safety hazards.
High maintenance cost: The frequency of manual inspections in remote areas is low, fault response is delayed, and mechanical parts are prone to wear and need to be replaced frequently.
Data integration is difficult: The lack of a standard signal output interface makes it difficult to seamlessly connect with the SCADA system (supervisory control and data acquisition system).
Product recommendation
GPT203 IP68 pressure transmitter, specially designed for outdoor pipeline pressure measurement, waterproof grade IP68, is suitable for harsh environment of long-term flooding, immersion, high humidity and temperature, alternating hot and cold, sewage corrosion, etc. The product adopts diffused silicon pressure core as sensitive component, and the built-in processing circuit converts the sensor millivolt signal into a standard analog or digital signal output, which can be directly connected to computers, control instruments, display instruments, etc.
Product Characteristics
High accuracy: Full range accuracy ±0.1%, long-term stability better than 0.2%FS/year.
Strong environmental adaptability: built-in temperature compensation chip (-40℃~85℃), protection grade is IP68, resistant to hydrogen sulfide corrosion (H₂S concentration ≤ 500ppm)。
Intrinsically safe: ATEX certified, explosion-proof mark ExiaIIC T6.
Intelligent integration: supports 4-20mA, 0-5V, RS485, IIC, etc., and can realize real-time monitoring of IoT platform when matched with modules.
Customer Case
Application Background
The West-East Gas Transmission Branch Project in China, it is required to monitor pressure along the pipeline. The pipeline is 230 kilometers long, passes through varied terrains such as plateaus and deserts, with the lowest temperature in winter being -35℃. It is necessary to implement over-pressure alarm (threshold value set at 6.4MPa) at 12 sub-transmission stations and 8 valve chambers along the route.
Solutions
1.Install GPT203 pressure sensor behind the filter of the sub-transmission station and in front of the pressure regulating valve to monitor the main pressure in real time. The pressure sensor has a range of 0~10Mpa and outputs a 4-20mA standard signal.
2.System integration: The GPT203 pressure sensor outputs a 4-20mA signal that is connected to the PLC controller. The alarm upper limit is set to 6.4Mpa. It is set to link the ESD emergency cutoff system, and the response time is less than 2 seconds. The conveying system is automatically cut off when the pressure exceeds the limit to protect the safety of the equipment.
3.Upload data to the cloud through the GRT102 wireless module to achieve real-time warning and remote monitoring on mobile phones.
Effects
1.Safety improvement: No leakage accidents caused by abnormal pressure occurred within 2 years after commissioning, and the failure rate was restored to 67% compared with the mechanical watch era.
2. Optimization of operation and maintenance costs: The sensor has a maintenance-free period of 5 years, reducing annual maintenance costs by approximately RMB 1.2 million.
3.Energy efficiency management: By combining pressure data to optimize compressor operating parameters, a single pipeline can save approximately 1.8 million kWh of electricity per year.